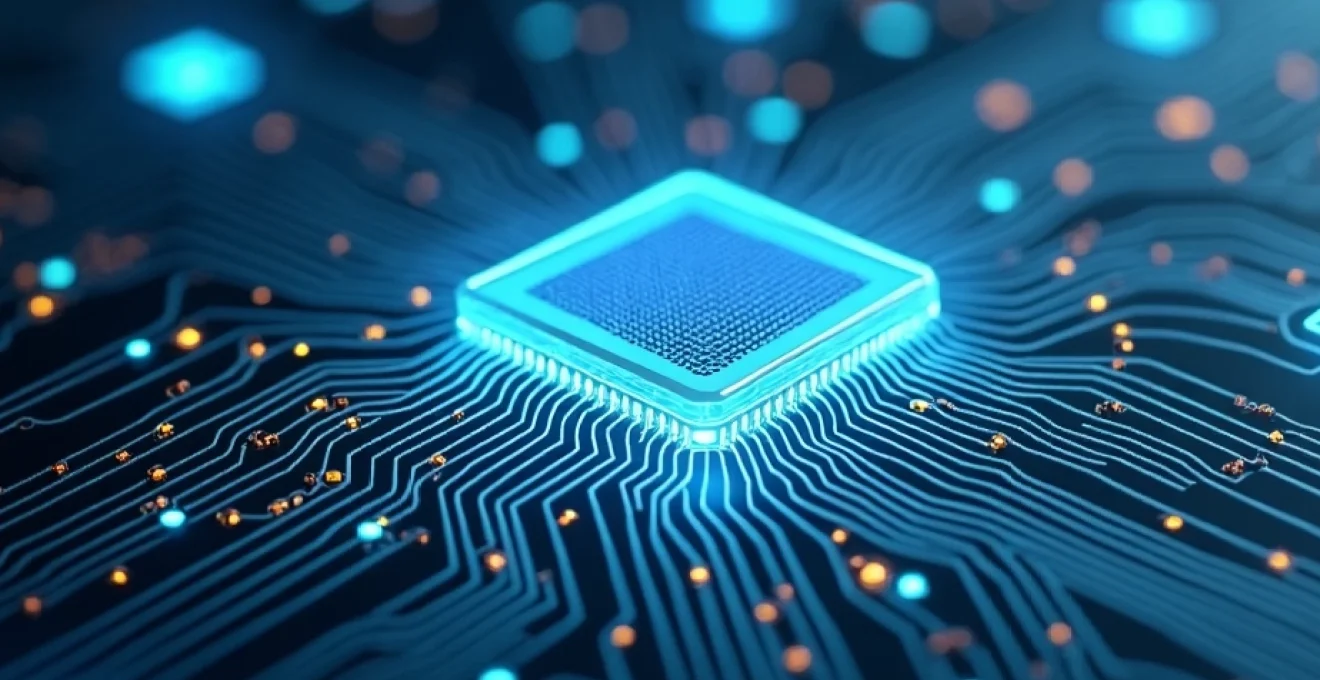
In der heutigen wettbewerbsintensiven Elektronikindustrie spielt die Kostenoptimierung eine entscheidende Rolle für den Erfolg von Unternehmen. Leiterplattenhersteller nehmen dabei eine Schlüsselposition ein, da sie maßgeblich die Gesamtkosten der Elektronikproduktion beeinflussen können. Durch innovative Fertigungstechniken, effizientes Design und strategische Partnerschaften eröffnen sich vielfältige Möglichkeiten, die Produktionskosten zu senken und gleichzeitig die Qualität zu steigern. Eine ganzheitliche Betrachtung der Wertschöpfungskette ermöglicht es, erhebliche Einsparpotenziale zu identifizieren und umzusetzen.
Optimierung von Leiterplattendesign für effiziente Fertigung
Ein durchdachtes Leiterplattendesign bildet die Grundlage für eine kosteneffiziente Fertigung. Durch die Berücksichtigung fertigungstechnischer Aspekte bereits in der Entwicklungsphase lassen sich signifikante Einsparungen erzielen. Dabei spielen verschiedene Faktoren eine wichtige Rolle, die es zu optimieren gilt.
Kompaktes Layout reduziert Materialverbrauch
Ein kompaktes Leiterplattenlayout trägt entscheidend zur Kostensenkung bei. Durch die geschickte Anordnung von Komponenten und Leiterbahnen lässt sich die benötigte Platinenfläche minimieren. Dies reduziert nicht nur den Materialverbrauch, sondern ermöglicht auch die Fertigung von mehr Leiterplatten pro Produktionscharge. Fortschrittliche CAD-Tools unterstützen Entwickler dabei, das Layout zu optimieren und Platzreserven optimal zu nutzen. Eine Verkleinerung der Leiterplattenfläche um nur 10% kann bereits zu Kosteneinsparungen von 5-8% führen.
Standardisierte Komponenten vereinfachen Bestückung
Die Verwendung standardisierter Komponenten bietet erhebliche Vorteile in der Fertigung. Einheitliche Bauteilgrößen und -formen erleichtern die automatisierte Bestückung und reduzieren die Komplexität des Fertigungsprozesses. Dadurch lassen sich Rüstzeiten verkürzen und die Effizienz steigern. Zudem ermöglicht die Standardisierung oft günstigere Einkaufskonditionen durch höhere Stückzahlen. Studien zeigen, dass der Einsatz standardisierter Komponenten die Bestückungskosten um bis zu 15% senken kann.
Minimierung von Layern spart Produktionskosten
Die Anzahl der Leiterplattenlagen hat einen direkten Einfluss auf die Fertigungskosten. Jede zusätzliche Lage erhöht den Material- und Arbeitsaufwand. Daher sollten Entwickler stets prüfen, ob sich die Funktionalität mit weniger Lagen realisieren lässt. Moderne Layouttechniken wie High-Density Interconnect (HDI) ermöglichen es, komplexe Schaltungen auf weniger Lagen unterzubringen. Die Reduzierung von sechs auf vier Lagen kann die Produktionskosten um 20-30% senken. Eine sorgfältige Abwägung zwischen Komplexität und Lagenanzahl ist entscheidend für die Kostenoptimierung.
Ein effizientes Leiterplattendesign ist der Schlüssel zur Kostensenkung in der Elektronikproduktion. Durch kompakte Layouts, standardisierte Komponenten und optimierte Lagenstrukturen lassen sich erhebliche Einsparungen erzielen.
Automatisierung in der Leiterplattenproduktion steigert Wirtschaftlichkeit
Die zunehmende Automatisierung revolutioniert die Leiterplattenproduktion und eröffnet neue Möglichkeiten zur Kostensenkung. Moderne Fertigungsanlagen ermöglichen höhere Durchsatzraten bei gleichzeitiger Qualitätssteigerung. Investitionen in automatisierte Prozesse zahlen sich langfristig durch geringere Personalkosten und eine verbesserte Wettbewerbsfähigkeit aus. Hier klicken, um mehr zu erfahren über innovative Automatisierungslösungen in der Leiterplattenfertigung.
Roboterbestückung erhöht Durchsatz und Präzision
Hochpräzise Bestückungsroboter haben die Leiterplattenfertigung revolutioniert. Sie arbeiten mit einer Genauigkeit von wenigen Mikrometern und erreichen Bestückungsraten von über 100.000 Komponenten pro Stunde. Im Vergleich zur manuellen Bestückung steigern sie den Durchsatz um ein Vielfaches bei gleichzeitiger Reduzierung von Fehlerquoten. Moderne Pick-and-Place-Maschinen passen sich flexibel an unterschiedliche Bauteilgrößen an und ermöglichen schnelle Produktwechsel. Der Einsatz von Roboterbestückung kann die Fertigungskosten um 30-50% senken und gleichzeitig die Qualität verbessern.
Automatische optische Inspektion sichert Qualität
Systeme zur automatischen optischen Inspektion (AOI) spielen eine zentrale Rolle bei der Qualitätssicherung in der Leiterplattenfertigung. Sie überprüfen bestückte Platinen auf Lötfehler, fehlende oder falsch platzierte Komponenten sowie andere Defekte. Hochauflösende Kameras und fortschrittliche Bildverarbeitungsalgorithmen ermöglichen eine zuverlässige Fehlererkennung bei Geschwindigkeiten von mehreren Quadratzentimetern pro Sekunde. AOI-Systeme reduzieren den Bedarf an manuellen Sichtprüfungen und senken die Fehlerrate in der Endmontage. Studien zeigen, dass der Einsatz von AOI die Qualitätskosten um bis zu 40% reduzieren kann.
Inline-Funktionstests identifizieren Fehler frühzeitig
Automatisierte Inline-Funktionstests ermöglichen eine frühzeitige Fehlererkennung direkt im Fertigungsprozess. Durch die Integration von Testschritten in die Produktionslinie lassen sich defekte Baugruppen schnell identifizieren und aussortieren. Dies verhindert, dass fehlerhafte Produkte in nachgelagerte Prozessschritte gelangen, und reduziert Nacharbeitskosten. Moderne Testsysteme kombinieren elektrische Prüfungen mit funktionalen Tests und decken so ein breites Spektrum möglicher Fehler ab. Der Einsatz von Inline-Funktionstests kann die Ausschussrate um bis zu 30% senken und die Gesamtproduktionskosten um 5-10% reduzieren.
Strategische Lieferantenauswahl für kostengünstige Leiterplatten
Die Auswahl der richtigen Lieferanten spielt eine entscheidende Rolle bei der Kostensenkung in der Leiterplattenproduktion. Eine durchdachte Beschaffungsstrategie ermöglicht es, Qualität und Wirtschaftlichkeit in Einklang zu bringen. Dabei gilt es, verschiedene Faktoren zu berücksichtigen und langfristige Partnerschaften aufzubauen.
Wettbewerbsfähige Preise durch Ausschreibungen erzielen
Regelmäßige Ausschreibungen für Leiterplattenaufträge schaffen Transparenz und fördern den Wettbewerb unter potenziellen Lieferanten. Durch die Einholung mehrerer Angebote lassen sich Marktpreise vergleichen und optimale Konditionen aushandeln. Dabei sollten neben dem Preis auch Faktoren wie Qualität, Lieferzuverlässigkeit und technische Kompetenz berücksichtigt werden. Eine professionelle Ausschreibung mit klar definierten Anforderungen ermöglicht es Lieferanten, passgenaue Angebote zu erstellen. Studien zeigen, dass strukturierte Ausschreibungsprozesse Einsparungen von 10-15% bei gleichbleibender Qualität ermöglichen können.
Rahmenverträge sichern langfristig attraktive Konditionen
Langfristige Rahmenverträge mit ausgewählten Lieferanten bieten Vorteile für beide Seiten. Hersteller profitieren von Planungssicherheit und stabilen Preisen, während Lieferanten ihre Kapazitäten besser auslasten können. Durch die Bündelung von Bedarfen lassen sich oft günstigere Konditionen aushandeln. Rahmenverträge sollten regelmäßig überprüft und an veränderte Marktbedingungen angepasst werden. Die Definition von Preisgleitklauseln ermöglicht es, Schwankungen bei Rohstoffpreisen zu berücksichtigen. Gut strukturierte Rahmenverträge können zu Kosteneinsparungen von 5-8% im Vergleich zu Einzelbestellungen führen.
Lieferantenbewertung stellt Zuverlässigkeit sicher
Ein systematisches Lieferantenmanagement ist entscheidend für eine stabile und kosteneffiziente Versorgung mit Leiterplatten. Regelmäßige Bewertungen anhand definierter Kriterien wie Qualität, Liefertreue und Innovationskraft ermöglichen es, die Leistung von Lieferanten objektiv zu beurteilen. Scorecards und Key Performance Indicators (KPIs) liefern wichtige Entscheidungsgrundlagen für die Lieferantenauswahl. Durch kontinuierliches Feedback und gemeinsame Verbesserungsinitiativen lässt sich die Zusammenarbeit optimieren. Eine professionelle Lieferantenbewertung kann die Gesamtkosten der Beschaffung um 3-5% senken und gleichzeitig die Versorgungssicherheit erhöhen.
Eine strategische Lieferantenauswahl kombiniert wettbewerbsfähige Preise mit hoher Qualität und Zuverlässigkeit. Durch langfristige Partnerschaften und kontinuierliche Optimierung lassen sich nachhaltige Kosteneinsparungen erzielen.
Innovative Leiterplattenmaterialien senken Elektronikproduktionskosten
Der Einsatz innovativer Materialien eröffnet neue Möglichkeiten zur Kostensenkung in der Leiterplattenfertigung. Moderne Substrate und Basismaterialien ermöglichen eine höhere Funktionsdichte bei gleichzeitiger Verbesserung der elektrischen und thermischen Eigenschaften. Dadurch lassen sich Produktionskosten senken und die Leistungsfähigkeit elektronischer Baugruppen steigern.
Hochtemperaturbeständige Substrate ermöglichen Miniaturisierung
Hochtemperaturbeständige Leiterplattenmaterialien wie Polyimid oder keramische Substrate eröffnen neue Designmöglichkeiten. Sie erlauben den Einsatz in Umgebungen mit hohen Temperaturen und ermöglichen eine stärkere Miniaturisierung durch engere Leiterbahnabstände. Dadurch lassen sich komplexe Schaltungen auf kleinerer Fläche realisieren, was den Materialverbrauch und die Fertigungskosten reduziert. Der Einsatz hochtemperaturbeständiger Substrate kann die Platinenfläche um bis zu 30% verkleinern und die Gesamtkosten um 10-15% senken.
Flexible Leiterplatten eröffnen neue Designoptionen
Flexible Leiterplatten auf Basis von Polyimid- oder Polyesterfolien bieten vielfältige Möglichkeiten zur Kostensenkung. Sie ermöglichen dreidimensionale Designs und lassen sich in komplexe Gehäuseformen integrieren. Dadurch können separate Verbindungselemente wie Kabel oder Steckverbinder eingespart werden. Flexible Leiterplatten vereinfachen zudem die Montage und reduzieren das Gesamtgewicht elektronischer Baugruppen. In der Automobilelektronik konnte durch den Einsatz flexibler Leiterplatten eine Gewichtsreduktion von bis zu 70% und eine Kostensenkung von 20-30% erzielt werden.
Halogenfreie Basismaterialien erfüllen Umweltauflagen kostengünstig
Halogenfreie Leiterplattenmaterialien gewinnen aufgrund strengerer Umweltauflagen zunehmend an Bedeutung. Sie bieten eine umweltfreundliche Alternative zu herkömmlichen Materialien und erfüllen die Anforderungen aktueller Richtlinien wie RoHS und REACH. Moderne halogenfreie Substrate weisen vergleichbare elektrische und mechanische Eigenschaften auf und lassen sich mit konventionellen Fertigungsprozessen verarbeiten. Der Einsatz halogenfreier Materialien kann die Entsorgungskosten um bis zu 40% senken und Umweltzertifizierungen vereinfachen.
Effizientes Testmanagement reduziert Leiterplattenausschuss
Ein durchdachtes Testmanagement spielt eine entscheidende Rolle bei der Kostensenkung in der Leiterplattenfertigung. Durch die frühzeitige Erkennung von Fehlern lassen sich Ausschussraten minimieren und teure Nacharbeiten vermeiden. Moderne Testverfahren kombinieren elektrische, optische und funktionale Prüfungen zu einer umfassenden Qualitätssicherung.
Der Einsatz von Flying-Probe-Testern ermöglicht eine flexible und kostengünstige Prüfung von Prototypen und Kleinserien. Diese Systeme arbeiten ohne teure Testadapter und passen sich schnell an neue Leiterplattendesigns an. Für größere Stückzahlen bieten In-Circuit-Tester (ICT) mit fest verdrahteten Prüfnadeln eine hohe Testabdeckung bei kurzen Prüfzeiten. Durch die Kombination verschiedener Testverfahren lässt sich eine Fehlererkennungsrate von über 99% erreichen.
Ein ganzheitlicher Testansatz berücksichtigt auch die Prüfung von Baugruppen unter realen Einsatzb
edingungen. Beschleunigte Alterungstests und Burn-In-Verfahren simulieren Langzeitbelastungen und decken potenzielle Schwachstellen auf. Ein gut strukturiertes Testmanagement kann die Ausschussrate um bis zu 50% reduzieren und die Gesamtkosten der Qualitätssicherung um 20-30% senken.
Die Integration von Testpunkten und Prüfstrukturen bereits im Leiterplattendesign vereinfacht spätere Tests und erhöht die Testabdeckung. Moderne CAD-Tools unterstützen Entwickler bei der Platzierung optimaler Testpunkte unter Berücksichtigung der geplanten Prüfverfahren. Durch die Abstimmung von Design und Testkonzept lassen sich Prüfzeiten verkürzen und Nacharbeitskosten minimieren.
Ein weiterer wichtiger Aspekt ist die statistische Prozesskontrolle (SPC) in der Leiterplattenfertigung. Durch die kontinuierliche Überwachung kritischer Prozessparameter können Abweichungen frühzeitig erkannt und korrigiert werden. Dies verhindert die Produktion fehlerhafter Chargen und reduziert den Prüfaufwand. Die Implementierung von SPC-Systemen kann die Ausschussrate um bis zu 40% senken und die Gesamtproduktivität um 10-15% steigern.
Ein effizientes Testmanagement kombiniert verschiedene Prüfverfahren und integriert Qualitätssicherung in den gesamten Fertigungsprozess. Durch frühzeitige Fehlererkennung und kontinuierliche Prozessoptimierung lassen sich Ausschussraten minimieren und Kosten nachhaltig senken.
Zusammenfassend lässt sich sagen, dass Leiterplattenhersteller durch die Optimierung von Design, Fertigung, Materialeinsatz und Qualitätssicherung erheblich zur Kostensenkung in der Elektronikproduktion beitragen können. Ein ganzheitlicher Ansatz, der alle Aspekte der Wertschöpfungskette berücksichtigt, eröffnet vielfältige Einsparpotenziale. Durch den Einsatz innovativer Technologien und strategische Partnerschaften können Hersteller ihre Wettbewerbsfähigkeit steigern und gleichzeitig die Qualität ihrer Produkte verbessern.
Wie sehen Sie die Zukunft der Leiterplattenfertigung? Welche Technologien werden Ihrer Meinung nach den größten Einfluss auf Kosten und Qualität haben? Teilen Sie Ihre Gedanken und Erfahrungen in den Kommentaren!