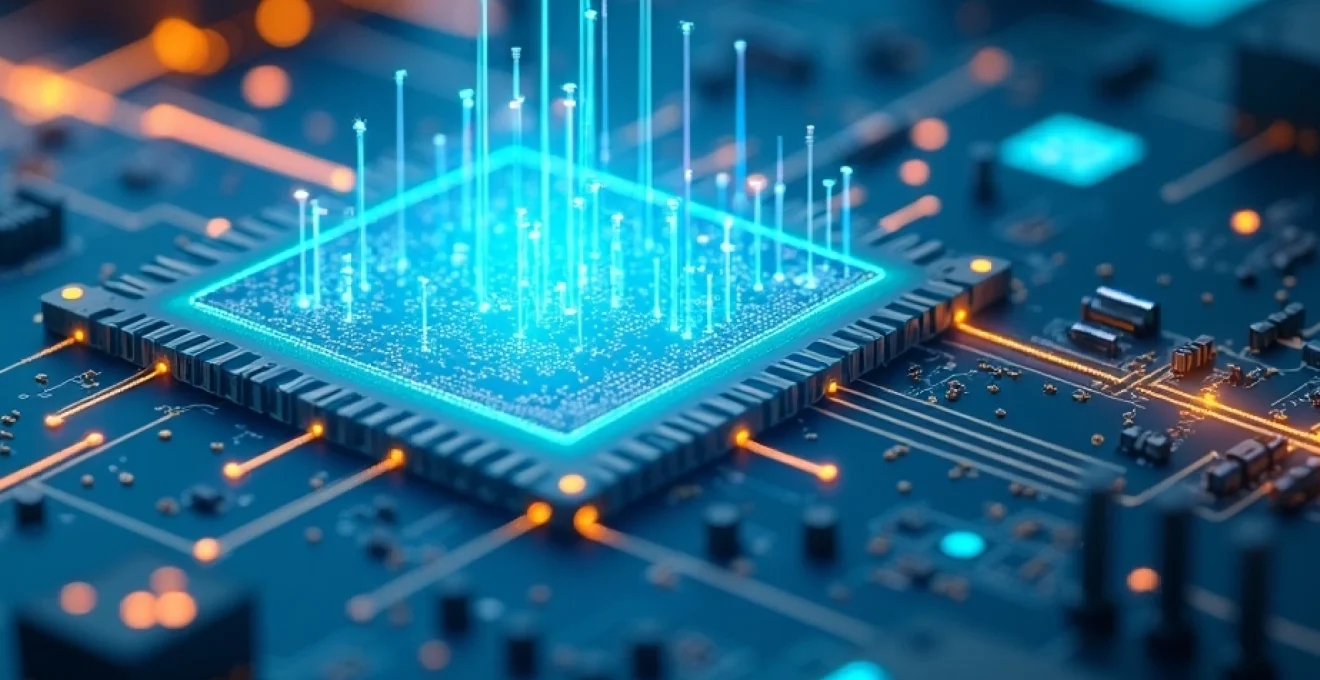
In der modernen Fertigungsindustrie gewinnt Flexibilität zunehmend an Bedeutung. Unternehmen stehen vor der Herausforderung, schnell auf Marktveränderungen zu reagieren und individuelle Kundenwünsche zu erfüllen. Die Produktion auf Abruf, auch als Pull-Produktion bekannt, erweist sich dabei als Schlüsselkonzept für eine agile und effiziente Fertigung. Sie ermöglicht es Unternehmen, Ressourcen optimal zu nutzen, Lagerbestände zu minimieren und gleichzeitig die Kundenzufriedenheit zu steigern. Doch wie funktioniert dieses Konzept in der Praxis und welche Vorteile bietet es gegenüber herkömmlichen Produktionsansätzen?
Grundlagen der Produktion auf Abruf (Pull-Produktion)
Die Produktion auf Abruf stellt einen Paradigmenwechsel in der Fertigungsindustrie dar. Im Gegensatz zur traditionellen Push-Produktion, bei der Waren auf Vorrat produziert werden, orientiert sich die Pull-Produktion am tatsächlichen Bedarf. Produkte werden erst dann hergestellt, wenn eine konkrete Nachfrage vorliegt. Dieser Ansatz reduziert nicht nur Überproduktion und Lagerkosten, sondern erhöht auch die Flexibilität des gesamten Produktionssystems.
Ein wesentlicher Vorteil der Pull-Produktion liegt in ihrer Fähigkeit, schnell auf Marktveränderungen zu reagieren. Unternehmen können ihre Produktion nahezu in Echtzeit an die Kundennachfrage anpassen. Dies ist besonders wertvoll in Branchen mit hoher Produktvielfalt oder schnell wechselnden Trends. Die Pull-Strategie ermöglicht es, Ressourcen effizient einzusetzen und gleichzeitig die Lieferzeiten zu verkürzen.
Die Implementierung einer Pull-Produktion erfordert jedoch eine gründliche Umstellung der Produktionsprozesse und der Unternehmenskultur. Mitarbeiter müssen geschult und Systeme angepasst werden, um den neuen Anforderungen gerecht zu werden. Trotz dieser Herausforderungen zeigen zahlreiche Erfolgsbeispiele, dass sich der Aufwand lohnt.
Just-in-Time (JIT) als Kernkonzept der flexiblen Fertigung
Das Just-in-Time-Prinzip bildet das Herzstück der Produktion auf Abruf. Es zielt darauf ab, Materialien, Komponenten und Produkte genau dann bereitzustellen, wenn sie benötigt werden. Dieser Ansatz minimiert Lagerbestände und optimiert den Produktionsfluss. JIT erfordert eine präzise Planung und enge Abstimmung mit Lieferanten, um Engpässe zu vermeiden und eine reibungslose Produktion zu gewährleisten.
Toyota Production System (TPS) als Vorreiter des JIT-Prinzips
Das Toyota Production System gilt als Pionier und Vorbild für die erfolgreiche Umsetzung des JIT-Prinzips. Toyota entwickelte dieses System in den 1950er Jahren, um die Effizienz zu steigern und Verschwendung zu reduzieren. Der Erfolg von Toyota inspirierte Unternehmen weltweit, ähnliche Ansätze zu adaptieren.
Das TPS basiert auf zwei Hauptsäulen: Jidoka (Autonomation) und Just-in-Time. Jidoka bezieht sich auf die Fähigkeit von Maschinen, Probleme zu erkennen und die Produktion automatisch zu stoppen. JIT sorgt dafür, dass jeder Prozessschritt nur das produziert, was der nächste Schritt benötigt. Diese Kombination führt zu einer hocheffizienten und flexiblen Produktion.
Kanban-Systeme zur Steuerung des Materialflusses
Kanban-Systeme sind ein wesentliches Werkzeug zur Umsetzung des JIT-Prinzips. Sie steuern den Materialfluss durch visuelle Signale, typischerweise in Form von Karten oder digitalen Anzeigen. Wenn ein Arbeitsplatz Material benötigt, sendet er ein Kanban-Signal an den vorgelagerten Prozess. Dies löst die Produktion oder Lieferung der benötigten Teile aus.
Moderne Kanban-Systeme nutzen oft digitale Technologien, um den Informationsfluss zu beschleunigen und die Transparenz zu erhöhen. Elektronische Kanban-Boards ermöglichen eine Echtzeitüberwachung des Produktionsstatus und erleichtern die Koordination zwischen verschiedenen Abteilungen und Lieferanten.
Reduzierung von Lagerbeständen durch bedarfsorientierte Produktion
Die bedarfsorientierte Produktion führt zu einer signifikanten Reduzierung von Lagerbeständen. Unternehmen produzieren nur das, was aktuell benötigt wird, und vermeiden so die Kosten für überschüssige Lagerbestände. Dies setzt jedoch voraus, dass die Lieferkette hocheffizient und zuverlässig funktioniert.
Die Vorteile geringer Lagerbestände sind vielfältig:
- Reduzierung von Kapitalbildung in Form von Lagerbeständen
- Verringerung des Risikos von Überalterung oder Beschädigung gelagerter Waren
- Optimierung der Lagerflächen und -kosten
- Erhöhte Flexibilität bei Produktänderungen oder -variationen
Implementierung von One-Piece-Flow in der Fertigungslinie
One-Piece-Flow ist ein Konzept, bei dem Produkte einzeln und kontinuierlich durch die Produktion fließen, anstatt in Batches gefertigt zu werden. Dieser Ansatz reduziert Wartezeiten und Zwischenlager und ermöglicht eine schnellere Reaktion auf Qualitätsprobleme.
Die Umsetzung von One-Piece-Flow erfordert oft eine Neugestaltung der Produktionslinie. Arbeitsplätze müssen so angeordnet sein, dass ein reibungsloser Fluss möglich ist. Mitarbeiter müssen in der Lage sein, flexibel verschiedene Aufgaben zu übernehmen. Der Einsatz von visuellen Managementtools wie Andon-Boards kann dabei helfen, den Produktionsfluss zu überwachen und Probleme frühzeitig zu erkennen.
Technologische Enabler für Produktion auf Abruf
Die Umsetzung einer flexiblen Produktion auf Abruf wird durch moderne Technologien erheblich erleichtert. Diese Technologien ermöglichen eine bessere Planung, Steuerung und Überwachung der Produktionsprozesse. Sie bilden das Rückgrat für eine agile und effiziente Fertigung im Zeitalter der Industrie 4.0.
Einsatz von Manufacturing Execution Systems (MES) zur Echtzeitsteuerung
Manufacturing Execution Systems (MES) spielen eine zentrale Rolle bei der Umsetzung einer Produktion auf Abruf. Diese Softwaresysteme ermöglichen eine Echtzeitüberwachung und -steuerung der Produktionsprozesse. Sie sammeln Daten aus verschiedenen Quellen und stellen sie in einer übersichtlichen Form dar, sodass Entscheidungsträger schnell reagieren können.
Ein modernes MES bietet folgende Kernfunktionen:
- Echtzeit-Datenerfassung und -analyse
- Produktionsplanung und -steuerung
- Qualitätsmanagement
- Ressourcenmanagement
- Leistungsanalyse und Reporting
Durch die Integration von MES können Unternehmen ihre Produktionsabläufe optimieren, Durchlaufzeiten verkürzen und die Produktqualität verbessern. Dies ist besonders wertvoll für die Umsetzung einer flexiblen Fertigung, da es eine schnelle Anpassung an veränderte Produktionsanforderungen ermöglicht.
Industrial Internet of Things (IIoT) für vernetzte Produktionsumgebungen
Das Industrial Internet of Things (IIoT) revolutioniert die Art und Weise, wie Produktionsumgebungen vernetzt und gesteuert werden. Durch die Verbindung von Maschinen, Sensoren und Systemen entsteht ein dichtes Netzwerk, das kontinuierlich Daten generiert und austauscht. Diese Vernetzung ermöglicht eine nie dagewesene Transparenz und Steuerungsmöglichkeiten in der Produktion.
IIoT-Technologien unterstützen die flexible Fertigung auf mehreren Ebenen:
- Erhöhte Transparenz durch Echtzeitdaten von Maschinen und Prozessen
- Verbesserte Vorhersagegenauigkeit für Wartung und Produktionsplanung
- Optimierung des Energieverbrauchs und der Ressourcennutzung
- Ermöglichung flexibler Produktionskonfigurationen durch vernetzte Maschinen
Die Integration von IIoT-Lösungen erfordert jedoch sorgfältige Planung und robuste Sicherheitsmaßnahmen, um Datenschutz und Betriebssicherheit zu gewährleisten.
Predictive Maintenance zur Minimierung von Ausfallzeiten
Predictive Maintenance nutzt Datenanalyse und maschinelles Lernen, um potenzielle Ausfälle von Maschinen und Anlagen vorherzusagen. Durch die kontinuierliche Überwachung von Maschinendaten können Wartungsarbeiten gezielt geplant und durchgeführt werden, bevor es zu einem Ausfall kommt. Dies reduziert ungeplante Ausfallzeiten und erhöht die Verfügbarkeit der Produktionsanlagen.
Die Vorteile von Predictive Maintenance sind vielfältig:
- Reduzierung ungeplanter Ausfallzeiten
- Optimierung der Wartungskosten
- Verlängerung der Lebensdauer von Maschinen und Anlagen
- Verbesserung der Produktionsplanung und -effizienz
Für eine erfolgreiche Implementierung von Predictive Maintenance ist eine umfassende Dateninfrastruktur erforderlich, die Sensordaten erfasst, speichert und analysiert. Zudem müssen Mitarbeiter geschult werden, um die Ergebnisse der Analysen richtig zu interpretieren und entsprechende Maßnahmen einzuleiten.
Advanced Planning and Scheduling (APS) für optimierte Produktionsplanung
Advanced Planning and Scheduling (APS) Systeme ermöglichen eine hochkomplexe und präzise Produktionsplanung. Sie berücksichtigen eine Vielzahl von Faktoren wie Kapazitäten, Verfügbarkeiten, Liefertermine und Prioritäten, um einen optimalen Produktionsplan zu erstellen. APS-Systeme sind besonders wertvoll für Unternehmen mit komplexen Produktionsumgebungen und häufig wechselnden Aufträgen.
Kernfunktionen von APS-Systemen umfassen:
- Kapazitätsplanung und -optimierung
- Materialbedarfsplanung
- Auftragspriorisierung und -sequenzierung
- Simulation verschiedener Produktionsszenarien
- Integration mit ERP- und MES-Systemen
Der Einsatz von APS-Systemen ermöglicht es Unternehmen, flexibler auf Kundenanforderungen zu reagieren und gleichzeitig die Produktionseffizienz zu maximieren. Sie bilden damit eine wichtige Grundlage für die Umsetzung einer Produktion auf Abruf.
Herausforderungen und Lösungsansätze bei der Implementierung
Die Umstellung auf eine Produktion auf Abruf bringt zahlreiche Herausforderungen mit sich. Unternehmen müssen ihre Prozesse, Technologien und oft auch ihre Unternehmenskultur grundlegend überdenken. Eine der größten Hürden ist oft der Widerstand gegen Veränderungen innerhalb der Organisation. Mitarbeiter müssen von den Vorteilen des neuen Systems überzeugt und in dessen Umsetzung eingebunden werden.
Ein weiterer kritischer Punkt ist die Integration neuer Technologien in bestehende Systeme. Die Implementierung von MES, IIoT oder APS-Lösungen erfordert oft erhebliche Investitionen und technisches Know-how. Unternehmen müssen sorgfältig planen, wie sie diese Technologien schrittweise einführen und mit ihren bestehenden Systemen verbinden können.
Die Umstellung auf eine Pull-Produktion kann auch zu Herausforderungen in der Lieferkette führen. Lieferanten müssen in der Lage sein, flexibel und schnell auf Bedarfsänderungen zu reagieren. Dies erfordert oft eine enge Zusammenarbeit und den Aufbau von Partnerschaften entlang der gesamten Wertschöpfungskette.
„Der Übergang zu einer Produktion auf Abruf ist kein Sprint, sondern ein Marathon. Es erfordert Geduld, kontinuierliche Verbesserung und ein tiefes Verständnis der eigenen Prozesse.“
Erfolgreiche Unternehmen setzen auf einen schrittweisen Ansatz bei der Implementierung. Sie beginnen oft mit Pilotprojekten in einzelnen Produktionsbereichen, um Erfahrungen zu sammeln und Prozesse zu optimieren, bevor sie das System auf das gesamte Unternehmen ausweiten. Schulungen und Change-Management-Initiativen spielen dabei eine zentrale Rolle, um die Akzeptanz bei den Mitarbeitern zu erhöhen.
Fallstudien erfolgreicher Produktion auf Abruf in der Industrie
Bosch Rexroth: Flexibilisierung der Hydraulikkomponentenfertigung
Bosch Rexroth, ein führender Anbieter von Antriebs- und Steuerungstechnologien, hat die Produktion auf Abruf erfolgreich in seiner Hydraulikkomponentenfertigung implementiert. Das Unternehmen nutzt ein hochflexibles Fertigungssystem, das es ermöglicht, über 200 verschiedene Hydraulikventile auf derselben Linie zu produzieren.
Durch den Einsatz von digitalen Technologien und intelligenten Vernetzungslösungen konnte Bosch Rexroth die Durchlaufzeiten um 30% reduzieren und die Produktivität um 10% steigern. Ein Schlüsselelement war die Einführung eines digitalen Shopfloor-Managements, das Echtzeitdaten zur Produktionssteuerung nutzt und eine schnelle Anpassung an Bedarfsschwankungen ermöglicht.
„Die Flexibilisierung unserer Fertigung hat es uns ermöglicht, schneller auf Kundenanforderungen zu reagieren und gleichzeitig unsere Effizienz zu steigern. Dies war ein entscheidender Schritt, um unsere Wettbewerbsfähigkeit in einem dynamischen Markt zu sichern.“
Siemens: Digitale Fabrik in Amberg als Vorzeigemodell
Die Siemens-Elektronikfabrik in Amberg gilt als Vorzeigemodell für die Industrie 4.0 und demonstriert eindrucksvoll die Möglichkeiten einer flexiblen Produktion auf Abruf. In dieser hochautomatisierten Fabrik werden jährlich über 15 Millionen Simatic-Produkte in mehr als 1.000 Varianten gefertigt – mit einer beeindruckenden Fehlerquote von nur 0,0012%.
Kernelemente der Amberger Fabrik sind:
- Vollständige Digitalisierung und Vernetzung der Produktionsprozesse
- Einsatz von KI-gestützten Systemen zur Produktionsoptimierung
- Flexible Fertigungslinien, die schnell auf Produktwechsel reagieren können
- Echtzeitüberwachung und -steuerung durch ein zentrales MES
Diese hochflexible Fertigungsumgebung ermöglicht es Siemens, Kundenwünsche innerhalb kürzester Zeit zu erfüllen und gleichzeitig eine hohe Produktqualität zu gewährleisten. Die Fabrik dient als Inspiration für viele Unternehmen weltweit, die eine ähnliche Transformation anstreben.
BMW Group: Modulare Produktion im Werk Spartanburg
Das BMW-Werk in Spartanburg, USA, ist ein Paradebeispiel für modulare Produktion und flexible Fertigung im Automobilsektor. In diesem Werk werden täglich bis zu 1.500 Fahrzeuge in verschiedenen Modellvarianten produziert, wobei jedes Fahrzeug individuell nach Kundenspezifikation gefertigt wird.
Zentrale Elemente der flexiblen Produktion in Spartanburg sind:
- Modulare Produktionslinien, die verschiedene Modelle parallel fertigen können
- Einsatz von autonomen Transportsystemen für flexible Materialflüsse
- Digitale Zwillinge zur Simulation und Optimierung von Produktionsprozessen
- Echtzeit-Datenanalyse zur kontinuierlichen Prozessverbesserung
Durch diese Ansätze konnte BMW die Produktionsflexibilität erheblich steigern und gleichzeitig die Effizienz verbessern. Das Werk ist in der Lage, schnell auf Nachfrageschwankungen zu reagieren und neue Modellvarianten ohne größere Umrüstzeiten in die Produktion zu integrieren.
Zukunftsperspektiven der flexiblen Fertigung
Künstliche Intelligenz zur autonomen Produktionssteuerung
Die Integration von Künstlicher Intelligenz (KI) in Produktionssysteme verspricht eine neue Ära der autonomen Fertigungssteuerung. KI-Systeme können komplexe Datenströme in Echtzeit analysieren und selbstständig Entscheidungen treffen, um die Produktion zu optimieren. Dies ermöglicht eine noch flexiblere und effizientere Anpassung an Marktveränderungen und Kundenanforderungen.
Potenzielle Anwendungsfelder für KI in der flexiblen Fertigung umfassen:
- Dynamische Produktionsplanung und -steuerung basierend auf Echtzeit-Marktdaten
- Vorausschauende Wartung mit präzisen Vorhersagen von Maschinenausfällen
- Autonome Qualitätskontrolle durch KI-gestützte Bildverarbeitung
- Optimierung von Energieverbrauch und Ressourceneinsatz
Mit fortschreitender Entwicklung von KI-Technologien werden Produktionssysteme zunehmend in der Lage sein, sich selbstständig zu optimieren und auf unvorhergesehene Ereignisse zu reagieren. Dies wird die Flexibilität und Anpassungsfähigkeit von Fertigungsunternehmen auf ein neues Niveau heben.
5G-Technologie für hochflexible Fertigungsumgebungen
Die Einführung von 5G-Netzwerken in industriellen Umgebungen wird die Möglichkeiten der flexiblen Fertigung weiter revolutionieren. Mit extrem niedrigen Latenzzeiten, hohen Datenübertragungsraten und der Fähigkeit, eine Vielzahl von Geräten gleichzeitig zu verbinden, schafft 5G die Grundlage für hochvernetzte und agile Produktionsumgebungen.
Vorteile von 5G für die flexible Fertigung:
- Echtzeitkommunikation zwischen Maschinen, Sensoren und Steuerungssystemen
- Ermöglichung von mobilen Robotern und flexiblen Produktionslinien
- Verbesserte Datenanalyse und Entscheidungsfindung durch schnellere Datenübertragung
- Unterstützung von Augmented Reality für Wartung und Schulung
Die Integration von 5G-Technologie wird es Unternehmen ermöglichen, ihre Produktionsumgebungen noch flexibler zu gestalten und schneller auf Veränderungen zu reagieren. Dies wird besonders in Industrien mit komplexen Produktionsprozessen und häufigen Produktwechseln von Vorteil sein.
Additive Fertigung als Enabler für On-Demand-Produktion
Die additive Fertigung, besser bekannt als 3D-Druck, entwickelt sich zunehmend zu einem Schlüsselelement der flexiblen Produktion auf Abruf. Diese Technologie ermöglicht die Herstellung komplexer Komponenten in kleinen Stückzahlen ohne die Notwendigkeit spezieller Werkzeuge oder Formen.
Potenziale der additiven Fertigung für die flexible Produktion:
- Schnelle Prototypenerstellung und Produktanpassung
- Dezentrale Produktion von Ersatzteilen on-demand
- Reduzierung von Lagerbeständen durch bedarfsgerechte Produktion
- Ermöglichung komplexer Geometrien und kundenspezifischer Designs
Mit der Weiterentwicklung der 3D-Drucktechnologie in Bezug auf Geschwindigkeit, Materialvielfalt und Präzision wird die additive Fertigung zunehmend in Produktionslinien integriert werden. Dies wird Unternehmen in die Lage versetzen, hochindividualisierte Produkte in kleinsten Stückzahlen wirtschaftlich zu produzieren und somit die Flexibilität ihrer Fertigung weiter zu steigern.
Die Zukunft der Fertigung liegt in der Kombination von digitalen Technologien, flexiblen Produktionssystemen und innovativen Fertigungsmethoden. Unternehmen, die diese Entwicklungen frühzeitig adaptieren, werden in der Lage sein, auch in volatilen Märkten erfolgreich zu agieren und sich einen entscheidenden Wettbewerbsvorteil zu sichern.